Information Center
Ultimate 2025 Beginner’s Guide to Metal Fabrication Machinery
Posted on May 05, 2025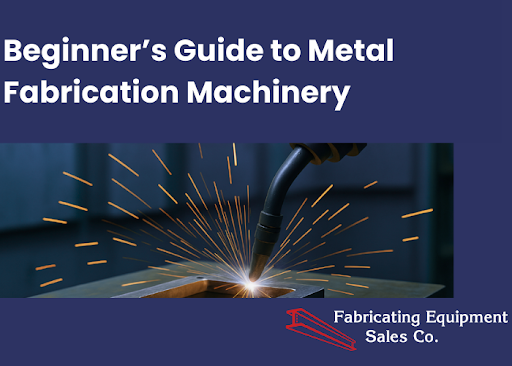
The metal fabrication industry stands at the heart of modern manufacturing, where advanced machinery transforms raw materials into precision components. Today’s fabrication shops rely on cutting-edge equipment—from CNC laser systems that handle complex geometries to industrial press brakes built for high-tonnage bending—to meet the demands of aerospace, automotive, and construction sectors.
This guide breaks down the essential machines that drive efficiency and quality in 2025, helping you select the right tools to turn metal stock into high-value products. Whether you’re investing in your first plasma cutter or automating an entire production line, understanding these systems is critical for staying competitive.
What Is Metal Fabrication?
Metal fabrication is the art and science of converting different metals—such as steel, aluminum, or copper (with excellent electrical conductivity)—into usable final products through controlled processes like cutting, bending, various welding techniques, and assembling.
Metal fabricators, the skilled professionals behind these tasks, employ a mix of manual expertise and advanced machinery to achieve a desired shape for components used in construction, automotive systems, and machinery. The industry thrives on precision, with metal fabrication shops often specializing in specific techniques, such as sheet metal fabrication for HVAC systems or metal casting processes for automotive parts.
2025 Common Metal Fabrication Processes
Metal fabrication relies on a series of interconnected techniques to transform raw metal materials into functional, market-ready products. These processes—ranging from cutting and bending to welding and finishing—serve as the foundation for creating everything from industrial machinery components to architectural structures.
Each method requires specialized tools and machinery to manipulate metal into a desired shape, whether through removing excess material, joining separate pieces, or altering structural properties.
Below, we explore the most widely used metal fabrication processes, emphasizing their applications, machinery requirements, and role in producing solid metal objects. Understanding these fundamentals equips businesses to select the right material and equipment that aligns with the project's requirements, complexity, and precision demands.
I. Cutting: Transforming Raw Metal into Workable Pieces
The fabrication process typically begins with cutting, where raw metal is transformed into usable shapes and sizes. Precision is critical at this stage, as it sets the foundation for all downstream processes like forming, welding, and assembly.
Advances in cutting technology—particularly CNC (Computer Numerical Control) and CAD software—have revolutionized this process, offering unparalleled accuracy, repeatability, and efficiency. These methods are essential not just for reducing waste but also for meeting tight tolerances in both prototyping and full-scale production.
Key methods include:
1. Laser Cutting
In laser cutting, a concentrated beam of intense light is employed to melt, incinerate, or evaporate metal following a specified route. Laser cutters are particularly beneficial for custom fabrication and rapid prototyping, as they allow fast iteration without tooling changes.
The technique is largely computer-controlled, using computer-aided design (CAD) and digital models in the design process, and therefore perfectly suited for accurate sheet metal manufacturing.
- Applications: Widely used in automotive, aerospace (including larger projects), electronics, and musical instruments that require intricate designs.
- Advantages: High accuracy, clean edges, and minimal burring. Enabling new possibilities in complex geometries with tight tolerances.
- Limitations: Not as effective with thicker metals beyond 25mm; reflective materials like copper and aluminum can pose challenges unless fiber lasers are used.
2. Plasma Cutting
Plasma cutting, a key cutting tool, involves forcing a jet of ionized gas (plasma) through a constricted opening at high speed. This plasma reaches temperatures of over 20,000°C, creating molten metal that is blown away from the cut.
Plasma systems are ideal for high-speed cutting in heavy fabrication settings where detail is less critical but productivity is paramount.
- Applications: Common in industrial machinery maintenance, shipbuilding, metal art, and construction equipment repair. Ideal for working with the most common metals: steel, aluminum, and copper.
- Advantages: Fast cutting speeds and effective with thick or layered metal. Can be used manually or with CNC plasma tables for precision.
- Limitations: Less precise than laser cutting, especially on thin materials. Cut quality may degrade with increased thickness.
3. Waterjet Cutting
Waterjet cutting employs a powerful stream of water, frequently combined with abrasive particles like garnet, to sever metal without producing thermal effects. This is particularly advantageous for materials prone to damage from heat.
Waterjet cutting is favored in various industries where structural integrity, edge quality, and versatility outweigh speed or cost.
- Applications: Aerospace components, custom brackets, titanium panels, and other parts where maintaining material properties is crucial.
- Advantages: No heat-affected zone (HAZ), which prevents warping or microstructural changes. Cuts different materials, including composites, stone, ceramics, and metals, without thermal distortion.
- Limitations: Slower cutting speed compared to plasma or laser; equipment is more expensive and maintenance-intensive.
4. Die Cutting/ Shearing
Shearing, also known as die cutting, involves applying a high-force blade across sheet metal to make straight-line cuts. Shearing is the go-to method when speed, simplicity, and cost-effectiveness are more important than design complexity.
The process is mechanical and often used in high-volume production environments.
- Applications: Used extensively in manufacturing HVAC panels, appliance parts, and enclosures where straight cuts are required.
- Advantages: Efficient for the mass production of standardized parts. Significant cost savings through low operational expenses and minimal material waste.
- Limitations: Limited to straight cuts; not suitable for complex shapes or thick materials. Edges may require secondary processing.
II. Bending and the Roll Forming Process: Shaping with Precision
After metal has been cut to the desired size, bending is often the next step in fabrication. This process involves reshaping flat metal into angles, channels, or curves without removing any material. Bending plays a critical role in creating structural components, enclosures, brackets, and frames across a wide range of industries.
After metal has been cut to the desired size, bending is often the next step in fabrication. This process involves reshaping flat metal into angles, channels, or curves without removing any material. Bending plays a critical role in creating structural components, enclosures, brackets, and frames across a wide range of industries.
1. Bending: Controlled Deformation through Force
Bending is a metal forming process that involves the application of force to deform a metal workpiece, usually into a specific angle or curved shape. This is typically achieved using press brakes, which are machines equipped with upper and lower dies designed to form metal into precise bends.
- Applications: Common in industries such as construction, automotive, aerospace, and industrial equipment manufacturing.
- Advantages: Precise angle control in the design phase, adaptable to small-batch or custom production runs, and compatible with a wide variety of metals, including aluminum, stainless steel, and carbon steel.
- Limitations: Overbending or springback can occur if material characteristics are not properly accounted for. Accuracy depends on tool setup, material thickness, and operator skill.
2. Roll Forming: Efficient Long-Length Bending
Roll forming is a continuous manufacturing process where long sheet metal strips pass through a series of rollers to shape metal, each performing an incremental part of the bend. The process creates consistent profiles over extended lengths, such as roofing panels, wall cladding, steel framing, and automotive trim.
Modern roll forming systems use various tools for inline operations like punching, notching, or cutting, playing a significant role in mass production, further enhancing efficiency in producing metal parts by eliminating the need for secondary processes.
Applications: Long, uniform shapes such as C-channels, Z-bars, hat sections, and other linear profiles used in construction, HVAC systems, transportation, and infrastructure.
Advantages:
- Efficiency: High-speed production with minimal manual intervention.
- Consistency: Excellent dimensional accuracy and repeatability over long runs.
- Material Integrity: Gradual bending reduces stress and cracking, maintaining the material’s mechanical properties.
Limitations: Best suited for high-volume production due to the cost of roller dies and setup. Not ideal for one-off or highly customized parts.
Essential Tools and Equipment for Metal Fabrication
As technology continues to advance, compact CNC plasma cutters now offer affordable solutions without sacrificing capability. Investing in the right machinery ensures efficiency and quality:
1. CNC Machines
Automate repetitive tasks like cutting metal, bending, and rolling, which is ideal for mass production in machine shops.
2. Press Brakes
Deliver consistent bends in sheet metal fabrication with programmable depth and angle settings.
3. Ironworkers
Fast shearing of plates and punching holes, some machines offer styles of forming tools.
4. Plate Shape and Slip Rolls
Rolling Shaped Sections, plates, or sheets into cylinders, rings, or spirals.
5. Saws
Band Saws or circular Saws for cutting shapes to length Burr Free, Ferrous and non Ferrous metals.
6. Plasma Cutting
Plasma cutting is a fast and economical way to remove material from plates as opposed to oxy-fuel cutting. Plasma units can also be mounted to a robotic arm for cutting I Beams, Channel, Angle, and Flat.
7. Water Jets
High-pressure water with the addition of abrasives can cut many types of material from glass to high tensile steel.
8. Laser’s
Flat material to tubing, and shapes can be cut with modern Fiber Lasers. High precision and speed
9. Shears Plate and Sheet
An inexpensive way of cutting parts to size.
Fabricating Equipment Sales: Serving Colorado and Wyoming Since 1973
Fabricating Equipment Sales, serving Colorado and Wyoming since 1973, is a trusted provider of high-quality machinery designed to enhance every stage of the fabrication process. Whether your business needs cutting-edge CNC machines, laser cutting equipment, or advanced welding stations, Fabricating Equipment Sales offers a comprehensive selection to meet the demands of various industries, including the aerospace industry and the automotive industry.
Why Choose Fabricating Equipment Sales?
- Wide Selection of Equipment: From Plasma Cutters to Press Brakes and Robots, our tools cater to all aspects of metal fabrication, ensuring that businesses can execute complex designs with precision.
- Proven Industry Expertise: With decades of experience, Fabricating Equipment Sales offers expert advice to help you select the right equipment for your specific needs, whether you're scaling production or fine-tuning custom projects.
- Reliable Support: Serving Colorado and Wyoming, we offer not just equipment sales but also ongoing support and service to keep your machines running smoothly, ensuring operational efficiency.
For businesses in Colorado and Wyoming, Fabricating Equipment Sales is the go-to source for premium metal fabrication tools that drive productivity and quality, making us an essential partner in any fabrication project.
To get the most suitable and cost-effective fabricating equipment for your needs, contact Fabricating Equipment Sales Co. today!
You can reach us by phone at (303) 466-7341 (Office) or (303) 550-0734 (Cell), via fax at (303) 465-2117, or by emailing jim@fabricatingequipmentsales.com.